BIBUS MENOS NOWOŚCI - Drukarki 3D
EOS wznawia produkcję kultowego systemu spieku proszków metalowych M280
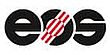
Firma EOS GmbH wznowiła produkcję systemu 3D do metalu EOSINT M280, który wykorzystuje technologię DMLS - Direct Metal Laser Sintering. Podjęcie takiej decyzji było spowodowane wysoką popularnością drukarki 3D do metalu EOSINT M280 w branży lotniczej i narzędziowej, w których konieczne jest zachowanie wysokiej jakości powierzchni oraz jednorodności struktury krystalicznej. Drukarka 3D EOSINT M280 przeszła czasochłonny proces kwalifikacji dla potrzeb produkcyjnych, w tym dla części medycznych i lotniczych, dzięki czemu wciąż cieszy się dużym popytem wśród obecnych użytkowników tych systemów. Wznowione systemy M280 oferowane są dodatkowo w bardzo korzystnej cenie.
Różnice między EOS M290 a EOSINT M280
Podstawowa różnica między nowym modelem EOS M290, a starszą drukarką 3D EOSINT M280, to wykorzystanie nowoczesnego, cyklonowego systemu filtracji gazu osłonowego, dzięki któremu wydłużony zostaje czas żywotności filtrów, nawet do ponad 1500 roboczogodzin. Kolejnym elementem, który rozróżnia oba systemy jest zastosowanie w M290 systemu kontroli jakości oraz dokumentacji procesu przetopu każdej z warstw, czyli EOSTATE 1.2 Quality Assurance Module. Obie maszyny oferują jednak taką samą, niezwykle wysoką jakość wytwarzanych za ich pomocą elementów.
Wznowienie wytwarzania systemu EOSINT M280 może okazać się niezwykle korzystne dla branży produkcyjnej. EOSINT M280 będzie oferowany w atrakcyjnej cenie, w porównaniu do takiej samej konfiguracji systemu M290.
Opis systemu EOSINT M280:
System do metalu EOSINT M280 wykorzystywany jest do niskoseryjnej lub jednostkowej produkcji metalowych części przy pomocy bezpośredniego przetapiania laserowego i spieku proszków metalowych, zwanego metodą DMLS (Direct Metal Laser Sintering). W ramach systemu stosowane mogą być takie materiały jak: stale narzędziowe, stale nierdzewne, aluminium, superstopy niklu, kobaltu oraz chromu, a także stopy tytanu. Branża przetwórstwa tworzyw sztucznych może wykorzystywać technologię DMLS jako metodę wytwarzania wkładek do form wtryskowych, wraz ze zintegrowanymi kanałami chłodzącymi o skomplikowanej geometrii. Swoboda w projektowaniu kanałów chłodzących pozwala technologii DMLS na skracanie cyklu wtryskowego w stosunku do standardowych rozwiązań chłodzenia, nawet o 60%. Jednorodny skurcz tworzywa oraz doskonały rozkład temperatur przekłada się na najwyższą jakość w dokładności wymiarowej elementów wtryskowych. Posiadając możliwość tworzenia części z materiałów takich jak TiAl6V4 czy stopy CoCrMo, technologia DMLS znajduje również zastosowanie w branży lotniczej i medycznej.
Parametry techniczne | |
---|---|
Wymiary maszyny: | 2200 x 1070 x 2290 mm |
Rekomendowane miejsce instalacji: | 4800 x 3600 x 2900 mm |
Waga: | ok. 1250 kg |
Zasilanie elektryczne: | 400VAC zabezpieczenie 32A (3 fazowe) |
Zasilanie sprężonego powietrza: | minimalne ciśnienie 7 bar przy wydatku 20m3/h |
Gaz osłonowy: | argon z butli lub azot ze zintegrowanej wytwornicy |
Pobór mocy: | max 8,5kW / typowo 3.2 kW |
Rozmiar przestrzeni roboczej:* | szerokość 250 mm*, głębokość 250 mm*, wysokość 325 mm* |
Laser: | włóknowy, iterbowy, moc użyteczna 200W lub 400W |
Grubość warstwy: | 0.02 mm, 0.03 mm, 0.04 mm, 0.05 mm, 0.08 mm (w zależności od przetwarzanego materiału) |
* W przypadku dużych detali należy uwzględnić termiczny skurcz liniowy i konieczność przeskalowania części w zależności od materiału w zakresie 0,02-0,1%.
Mikroprzetop proszków metalowych w technologii MLS już dostępny w Polsce
Obecnie zaobserwować można zmieniające się trendy w ramach technologii przyrostowych, a mianowicie ich przechodzenie ze sfery innowacyjnej do strefy przemysłowej w coraz większym zakresie. Technologie FDM, SLS czy też SLA w przemysłowych wersjach stosowane są do produkcji małoseryjnej lub indywidualnej oraz przy produkcji narzędzi, takich jak modele do odlewów traconych, formy wtryskowe, sprawdziany metryczne czy też uchwyty montażowe. Poszczególne branże przemysłowe stosują sprawdzone technologie addytywne, które zostały przez nie przetestowane oraz których zalety wykorzystano w praktyce. Równocześnie producenci maszyn przyrostowych stale rozwijają swoje produkty w zakresie materiałów, oprogramowania, optymalizacji procesu produkcyjnego, czy wzornictwa w postaci kolejnego wydania poszczególnych maszyn. Przykładem jest drukarka 3D P3 firmy EOS, która jest stale rozwijana od 1996 roku. Obecny model P396 jest już jego siódmą wersją.
Podobną sytuację można zaobserwować nie tylko w dziedzinie systemów przetwarzających tworzywa sztuczne, lecz także w zakresie maszyn do przetapiania proszków metalowych, gdzie nieustannie optymalizowana jest konstrukcja oraz parametry produkcyjne. W efekcie powstała technologia Micro Laser Sintering (MLS) czyli mikroprzetop proszków metalowych, rozwijany przez firmę 3D Micro Laser Sintering. Początki projektu sięgają 2006 roku, gdy firma 3DMicromac zajmująca się precyzyjną obróbką laserową oraz firma EOS rozpoczęły współpracę przy opracowaniu systemu do przyrostowego wytwarzania elementów w skali mikro z proszków metali.
Pierwszy element na systemie prototypowym w skali mikro z 2007r. - sześcian, w którym najmniejsze otwory miały wymiar 0,3 x 0,3 mm:
Rozwiązania firmy 3D MicroPrint
Parametry systemu µ60
W kolejnych latach skupiono się na optymalizacji parametrów produkcyjnych, poprawie konstrukcji systemu oraz testach eksploatacyjnych i aplikacyjnych. Doprowadziło to w 2013 do powstania firmy 3DMicroPrint oraz utworzenia komercyjnego systemu produkcyjnego µ60, dającego nowe możliwości produkcyjne. Charakteryzuje się on cylindryczną komorą ø 57 mm i 30 mm w osi Z. Grubość warstwy waha się w przedziale od 2 do 5 µm, a średnica lasera do zaledwie 30 µm, dzięki czemu można osiągnąć ścianki o grubości 0,32 mm. Cały proces jest szczelny i odbywa się w osłonie argonu z powodu bardzo małej ziarnistości proszku - poniżej 5 µm. Materiałami przetwarzanymi jest stal nierdzewna 316L i molibden, a wkrótce tytan i stale wysokostopowe. MLS umożliwia tworzenie spiralnych otworów o średnicy 0,1mm. Chropowatość powierzchni po wytworzeniu wynosi Ra=2 µm; Rz=13 µm, a w wyniku dodatkowej obróbki może osiągnąć nawet 0,7 µm.
MLS wprowadza technologie addytywne do świata mikro. Jest to kolejny, wyższy poziom przyrostowego przetwarzania stopów metali.
System seryjny DMP60GP
Rok 2016 to czas na wdrożenie systemu seryjnego DMP60GP, posiadający komorę roboczą o wymiarach 27 x 27 x 20 mm. Jest to mniejsze, kompaktowe rozwiązanie produkcyjne dla jednostek badawczo - rozwojowych, zapewniające sprawdzone parametry pracy i powtarzalność systemu µ60, z poprawioną ergonomią pracy użytkownika. DMP60GP to już 4. generacja systemu wykorzystującego technologię MLS, wytwarzająca precyzyjne elementy mikro z proszków metali.
Aplikacje w technologii MLS wykorzystywane są głównie w dziedzinie medycyny, wytwarzania mikronarzędzi chirurgicznych, struktur skafoldowych czy też endoprotez, takich jak stenty. Technologia ta wykorzystywana jest także w tworzeniu mikrowymienników ciepła z dużą powierzchnią wymiany przy małej objętości części. Mikromieszalniki i reaktory to następne struktury możliwe do wytworzenia w ramach inżynierii procesowej. Mikromechanika jest więc głównym obszarem zastosowań technologii MLS, lecz może być ona także stosowana w jubilerstwie przy wytwarzaniu drobnych, ażurowych elementów ozdobnych.
Ciekawym elementem było wykonanie mikrodyszy, która służy do cięcia kruchych materiałów półprzewodnikowych, takich jak SiC. Jej konwencjonalna konstrukcja składała się z 7 elementów, a czas wykonania wynosił 4 tygodnie. Technologia MLS umożliwiła stworzenie konstrukcji jednoelementowej, zoptymalizowanie jej o nowe funkcje, a także skrócenie czasu produkcji do 2 dni, dzięki czemu koszty produkcji obniżyły się o 60%. Średnica dyszy wynosi 0,24 mm, a grubość ścianek - 0,2 mm.
Firma BIBUS MEMOS, będąca od ponad dekady w branży 3D, jest partnerem 3DMicroPrint na terenie całego kraju. Jeśli są Państwo zainteresowani powyższymi rozwiązaniami zachęcamy do współpracy.
Więcej informacji można uzyskać na naszej stronie: www.drukarki3d.pl